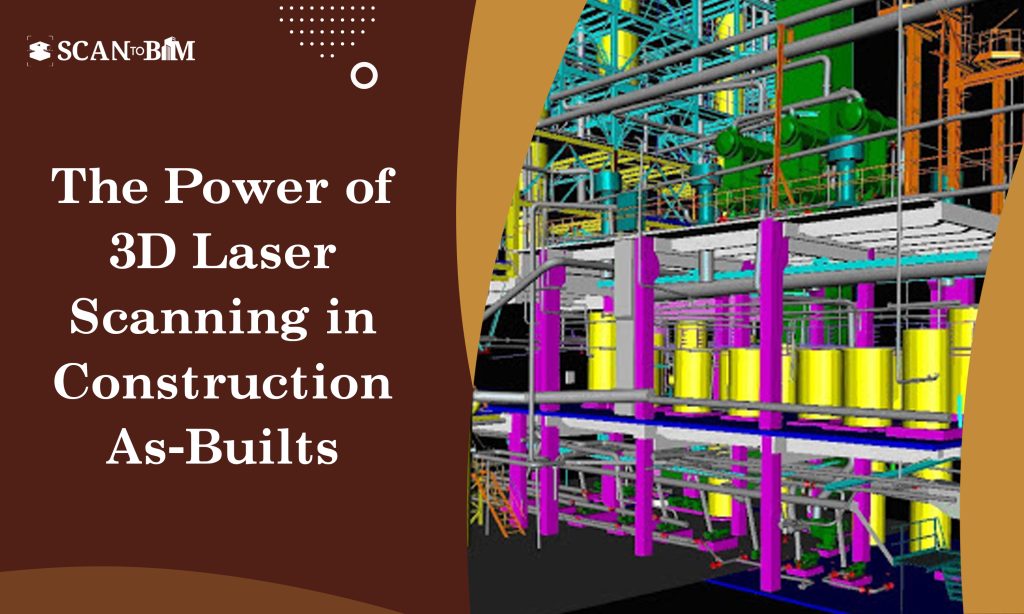
In the world of construction, efficiency is paramount. Every project involves numerous stakeholders, complex designs, and tight deadlines. Amidst this complexity, accurate as-built documentation is crucial for ensuring project success, facilitating communication among teams, and mitigating risks. Traditionally, this process has been lengthy and susceptible to mistakes. However, with the advent of 3D laser scanning technology, the construction industry is experiencing a revolution in as-built documentation.
Understanding As-Built Documentation
Before getting into the briefs about the benefits of 3D laser scanning, let’s first understand what as-built documentation entails. As-built documentation is the final set of drawings and documents that precisely depicts the completed construction project. It serves as a comprehensive record of all modifications, deviations, and actual conditions encountered during construction. This documentation is vital for future renovations, maintenance, and compliance purposes.
Challenges in Traditional As-Built Documentation
In the past, generating accurate as-built documentation has been a tedious and lengthy process packed with challenges:
- Manual Measurements: Traditional methods rely heavily on manual measurements, which are prone to human error and inaccuracies.
- Time-Intensive: Creating detailed as-built documentation manually requires significant time and resources, leading to delays in project timelines.
- Limited Accuracy: Conventional surveying techniques often lack the precision needed to capture intricate details and complex geometries accurately.
- High Costs: The expenses associated with hiring surveying teams and the potential for rework due to inaccuracies can significantly inflate project costs.
The Solution: 3D Laser Scanning
Enter 3D laser scanning—a game-changer in the area of as-built documentation. This innovative technology utilizes laser beams to rapidly capture precise 3D measurements of existing structures and environments. Here’s how it revolutionizes the as-built documentation process:
- Speed and Efficiency: 3D laser scanning dramatically accelerates the documentation process. In mere minutes, it can gather millions of data points, drastically cutting down the time needed for on-site measurements and data collection.
- High Precision and Accuracy: Unlike traditional methods, which are susceptible to human error, 3D laser scanning offers unparalleled accuracy. It captures precise measurements of even the most intricate details, ensuring that the final documentation reflects the true conditions of the project with availing the apt Scan to CAD Services.
- Comprehensive Data Capture: With 3D laser scanning, construction teams can capture detailed information about the entire project site, including structural elements, MEP (mechanical, electrical, plumbing) systems, and architectural features. This comprehensive data allows for a thorough understanding of the current conditions, reducing the risk of oversights and discrepancies.
- Streamlined Collaboration: By generating detailed 3D models of the as-built environment, laser scanning facilitates better communication and collaboration among project stakeholders. Designers, engineers, contractors, and clients can easily visualize the project in its current state, identify potential clashes or conflicts, and make informed decisions to streamline the construction process by using Scan to BIM Services.
- Cost-Effectiveness: Although the upfront investment in 3D laser scanning technology might appear substantial, its long-term cost-effectiveness is undeniable. By reducing rework, minimizing errors, and accelerating project timelines, laser scanning ultimately leads to cost savings throughout the construction lifecycle.
Real-World Applications
The versatility of 3D laser scanning makes it applicable across various stages of the construction process:
- Pre-Construction Planning: Before breaking ground, laser scanning can be used to conduct detailed site surveys, assess existing conditions, and inform the design process. This proactive stance helps in pinpointing potential challenges quite early, enabling more informed decision-making and risk mitigation strategies.
- Construction Monitoring: Throughout the construction phase, laser scanning provides real-time insights into project progress and quality control. By comparing scan data with design models, construction teams can identify deviations, monitor structural integrity, and ensure compliance with specifications.
- As-Built Documentation: Of course, the most significant application of 3D laser scanning lies in generating accurate as-built documentation. By capturing the final state of the project with precision and detail, laser scanning creates a valuable asset for facility management, future renovations, and regulatory compliance.
Conclusion
In the world of architecture and construction, where time is critical, precision is imperative and accuracy is non-negotiable, 3D laser scanning emerges as a transformative technology. By revolutionizing the as-built documentation process, it enables construction teams to work more efficiently, communicate more effectively, and deliver higher-quality projects. In AEC industry, the technology like 3D laser scanning stands out as a cornerstone of modern construction practices, driving progress, and enhancing outcomes for projects of all scales.